In the realm of seafaring vessels, noise generated by propulsor systems manifests in two distinct forms: onboard noise, perceptible within the confines of the vessel, and underwater radiated noise (URN), which resonates beneath the surface. While historical attention has centered on onboard noise, URN has emerged as a growing concern in recent decades. At Steerprop, we've embraced a proactive ethos, adopting a "design for low noise" strategy that integrates noise reduction considerations across all stages of design and manufacturing. This approach not only benefits onboard comfort but also mitigates the impact on URN.
The Impact of URN
While onboard noise may disrupt passengers or crew members, URN poses a more significant threat to fragile underwater ecosystems. Sensitive regions like the Arctic and Antarctic are particularly susceptible to URN disturbances, potentially impacting marine life and habitats. Recognizing this, entities like the Vancouver Fraser Port Authority have instituted incentives for ships meeting URN criteria, mindful of the well-being of local whale and mammal populations. Worldwide, fishing vessels and research ships alike are battling with URN's effects, from altering fish behavior to compromising underwater signal measurements. Classification societies have responded by introducing "quiet class" notations, initially addressing onboard noise but increasingly encompassing URN considerations. While URN classification remains relatively limited, industry trends suggest a growing emphasis on incorporating URN targets into new vessel designs, possibly culminating in future regulatory mandates.
The Quest for Silence
To meet the demand for vessels with reduced URN levels, designers and shipyards must carefully address all major noise sources. A tailored approach, customized to each vessel's design and operational requirements, is paramount. Propulsion systems represent a focal point, with efforts concentrated on minimizing noise from propellers and drive trains. Propeller-induced noise stems from water cavitation, while drive trains contribute mechanical and electrical noise. Steerprop's contra-rotating propulsion (CRP) system tackles both fronts by employing dual propellers with lower loading to mitigate cavitation, alongside LM units that integrate a permanent magnet motor to reduce drive train noise. Moreover, advancements in propulsion technology, such as the CRP, not only enhance efficiency but also inherently curb URN emissions by minimizing cavitation.
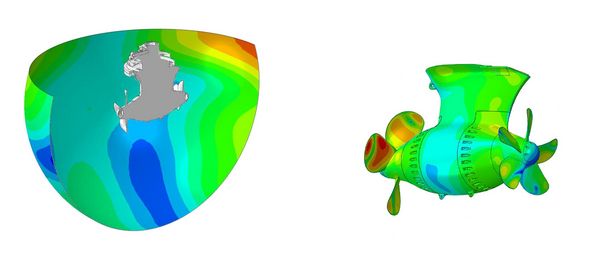
Advancing Noise Control
Beyond product development, collaborative research endeavors are instrumental in deepening our understanding of noise dynamics and mitigation strategies. Through partnerships with organizations like Finland-based ATA Gears and Luode Oy, we've delved into noise excitation mechanisms and conducted comprehensive noise measurements on various vessels. Despite progress, challenges persist, magnified by the scarcity of publicly available URN data. However, our commitment to a holistic noise control approach remains steadfast, fueled by ongoing research and an unwavering dedication to meeting the evolving needs of our clients.
Enhancing Tunnel Thrusters for Low URN Levels
In our pursuit of low URN levels, tunnel thrusters represent another vital consideration, not only for their contribution to URN but also for their impact on onboard noise during maneuvering. Acknowledging the hydrodynamic complexities inherent in tunnel thrusters, we're actively exploring optimization strategies, including fine-tuning propeller geometry and implementing innovative solutions to minimize noise emissions. Our objective is clear; to ensure tunnel thrusters operate with the utmost silence without compromising performance.